几种α型高强石膏生产方法介绍
几种α型高强石膏生产方法介绍
宁夏博得石膏研究院 王立明 陈兴福 王凯 王伟
摘要:本文主要对蒸压法及水热法生产α型高强石膏的几种工艺方法及其优缺点进行介绍,并通过几种工艺方法生产项目的实施数据,对不同工艺方法生产的α型高强石膏粉的性能及成本进行对比分析。
关键词:α型高强石膏 蒸压法、半干法、水热法、带压水热法、常压水热法
一、综述
石膏基建材具有轻质、高强、节能、环保、与人及环境融合性好等特点,是公认的生态建材、绿色建材,被广泛的应用于各个行业,在人们的日常生活和国民经济中发挥着越来越重要的作用。
随着经济发展,人们对居住环境及要求的提高,石膏材料作为墙体材料、装饰装修材料、功能性材料等大量应用于人们的日常生活和工业生产中;纸面石膏板、石膏砌块、石膏条板、抹灰石膏、石膏腻子、粘贴石膏、石膏线条、石膏装饰板、石膏吊顶板、石膏模盒、石膏浮雕、自流平石膏、石膏装配式建筑等成为人们生活中经常见到或用到的材料。陶瓷模具、工业模具、齿科石膏、绷带石膏、精密铸造、工艺美术石膏、玩具石膏、石膏晶须、硫酸钙抗静电地板、特种地板、GRG、3D打印、食用添加剂、工业填料等也成为石膏材料的重要用途。
随着石膏产制品用途的拓展及部分领域对石膏材料的性能指标要求的不断提高,α型高强石膏的用途得到了大幅度拓展,α石膏被广泛的应用于陶瓷模具、精密铸造、GRG制品、自流平砂浆、特种地板、齿科石膏、石膏工艺品、石膏制品等诸多领域;同时,不同应用领域对α型高强石膏有着不同的性能要求和成本承担范围,不同生产原料、不同生产方法又对α型高强石膏的性能指标和生产成本起着决定性作用。因此,针对不同的原料特性和产品要求,了解和选择与之匹配的α型石膏的生产方法和设备,可以在**产品性能和发挥原料价值的基础上有效的降低生产成本。
二、α型高强石膏的生产方法及特点
α型高强石膏的生产方法按照生产过程采用的介质可以分为两类:蒸压法和水热法。蒸压法是指在一定压力的饱和蒸汽介质中石膏由二水状态转化为α型半水状态的方法,蒸压法根据原料状态又可分为干法生产工艺和半干法生产工艺;水热法是指二水石膏在水溶液介质中完成由二水石膏至半水石膏的晶体转化过程,水热法根据水溶液的状态分为高压水溶液法和常压水溶液法;以上各类生产方法中,除干法蒸压法不采用转晶剂技术外,其余生产方法均需采用转晶剂技术作为配套。转晶剂也称为媒晶剂,是根据原料特性由一种或多种能够影响石膏晶体生产方向、形状和大小的有机盐、无机盐及有机酸等物质。因石膏原料种类较多,各类石膏成分及杂质含量各不相同,原料细度、类别、组成成分、杂质成分等均会对转晶效果产生影响,因此,对不同的原料类别甚至同一类不同杂质组成的原料,都需要根据自身特性进行调整,才能得到能够适应于该原料的*佳转晶剂配方技术,只有调整出*佳转晶剂技术,才能在合适的生产条件下生产出性能*佳的α型高强石膏产品。
1、蒸压法
蒸压法生产α型高强石膏的工艺方法根据具体原料状态又分为干法蒸压法技术和半干蒸压法技术。
1)干法蒸压法技术 是一种传统的α石膏生产技术,也就是俗称的蒸压法。该方法主要是以一定压力的饱和水蒸汽为介质,利用水蒸气介质的压力及热量,完成二水石膏晶体结构的转化和脱水,形成α型半水石膏晶型结构。该技术方法不采用转晶剂辅助,因此所采用的原料必须具有一定的粒度,粒度过小,容易造成蒸压后颗粒粘接;粒度过大,不易蒸透,产生生料。因此干法蒸压法主要应用于天然石膏为原料生产α型高强石膏。干法蒸压法根据具体烘干工艺分为一步法和二步法,一步法是将蒸压和烘干两个过程集成在一个设备内完成的工艺;二步法是指利用两个设备分别完成蒸压和烘干过程;
一步蒸压法的主要生产设备是立式蒸压釜,也叫脱水器,一步蒸压法及设备是宁夏建材研究院的研究成果,自上世纪80年代推出以来,先后在国内推广转让30余条生产线,经过不断的优化改进,仍然是目前天然石膏生产α型高强石膏工艺*简单、控制*稳定、生产成本*低的生产方法。 一步蒸压法具有如下特点:
⑴原料适应范围宽,对纯度大于75%以上的天然石膏原料,均可生产α型高强石膏,纯度的高低和杂质的类别仅影响强度等指标,不会影响生产过程的稳定性。对不同纯度的原料,均可调整生产出能够体现原料品位和特性的强度值;
⑵生产过程简单,产品质量稳定 ;该方法生产中,不需要转晶剂技术辅助,仅需要控制物料粒度、蒸汽压力、温度、时间等参数;蒸压和烘干在一个设备内完成,中间无影响及干扰因素,质量稳定性高。
⑶生产成本低,产品质量高;生产过程不采用转晶剂,比其它方法减少了转晶剂成本。生产过程集成在一个设备完成,质量干扰因素少,产品性能指标高,对95%以上的高纯度天然石膏原料,产品2小时抗折强度可达到8MPa以上;
⑷因蒸压及烘干集成在一个设备内完成,产品生产周期较长,但设备产量低,适合小规模高品质产品的生产;
二步法是采用蒸压釜完成石膏的蒸压过程,蒸压完成后石膏卸出蒸压釜,送入烘干设备直接烘干。也有将出蒸压釜的石膏自然晾晒至表面干燥后经破碎后再次煅烧的,该工艺因晾晒过程中会造成转化的α半水石膏再次水化成二水石膏,煅烧后实际形成的是α和β的混合石膏相,产品性能指标一般较低,会略高于同类原料生产的β石膏产品;
蒸压法高强石膏的晶体图片如下:
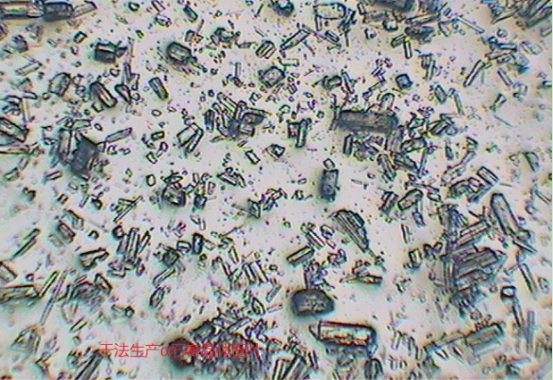
2)半干法
半干蒸压法即通常的半干法,是指将粉状或较小颗粒与粉状混合的石膏原料与转晶剂溶液进行均匀混合,混合后原料总体含水率一般保持在20%以内的半干状态,将这种半干状态的石膏原料直接送入转晶设备,在一定压力的饱和水蒸气介质下进行转晶或造粒后进行转晶的方法称为半干法。
宁夏建材研究院*早在2000年研制成功的利用天然石膏粉磨至一定细度后与转晶剂溶液混合后造粒,在一定饱和水蒸气压力条件下蒸压形成1:1—1:3的短柱状晶体生产K型超硬石膏,产品经过粉磨后标准稠度可达到25-35%,2小时抗折强度可达到5-7MPa;干抗压强度可达到60-80MPa;宁夏建材研究院并利用该技术建设年产5000吨生产线一条,生产该类产品,质量较为稳定,产品用于工艺品、铸造、原模等;但由于该方法生产过程中需要造粒成型,生产效率较低,生产规模小,成本相对较高;
宁夏博得石膏研究院在以上半干法的基础上,经过不断完善,研发成功了不需要造粒成型的半干法生产工艺—混合蒸压转晶技术,该方法可对与转晶剂混合均匀的含水率5-20%的粉状或一定粒度与粉状的混合料直接进行转晶,无需造粒或配浆等工序。
混合蒸压转晶半干法生产α型高强石膏粉的生产工艺流程主要包括如下几个部分:
混合工序 该工艺方法对原料的要求范围比较宽,因此,对粒度小于1mm,含水率低于20%的副产石膏原料均可直接进行配料;混合工序是该工艺的重要环节之一,主要是将原料与转晶剂(或转晶剂溶液)计量后,通过混合设备进行均匀混合的过程;混合的均匀程度直接决定转晶剂是否能够均匀分散至物料中,决定整个物料转晶均匀性从而形成以柱状晶体为主的晶型的主要要素。因此,**计量的**性和混合的均匀性非常主要。
蒸压转晶 该过程主要是通过向转晶设备内通入一定压力和温度的饱和水蒸汽,使设备内的物料处于饱和水蒸汽介质中,并通过蒸汽保持合适的转晶温度,从而通过转晶剂、蒸汽压力及温度的共同作用,使物料颗粒发生溶解再结晶,由无规则的颗粒形状重新生长为以六方短柱状晶体为主体(长径比1:1—1:3)的,以少量其它晶体(球状、棒状、纤维状等)为辅助的混合晶体形态;并形成大小不同的具有一定级配的晶体;由于半干状态下转晶剂离子不能形成自由迁移的完全均匀状态,各物料颗粒之间所吸附的转晶剂离子浓度存在一定的差异而导致的,但由于混合阶段要求的均匀性,则可以形成一定程度上的均一性,达到以短柱状晶体为主体的特点。转晶效果的主要影响因素为转晶剂配方、温度及压力,转晶剂配方是根据物料特点预先试验确定的,一般在生产前已经多次验证确认,而温度及压力则是生产过程中需要严格监控的参数,不同的物料、不同的配方所对应的*佳温度和压力参数均存在一定的差异;
烘干 蒸压转晶后,物料已经完成了从二水到半水石膏的转变,完成了晶体形态的转化,属于实际意义上的α型半水石膏。但脱出的结构水及物料表面的附着水仍然吸附在物料颗粒上,需要尽快的烘出,以避免逆反应对产品的影响。因此在烘干过程需要**合适的温度,仅烘干而不需要对物料产生二次煅烧,导致脱去剩余的结晶水;一般,由于转晶非常完备,物料比表面积大幅度缩小,达到转晶要求的物料活性很低,逆反应速度很慢,出转晶器物料2小时之内的逆反应对产品性能影响很小,而4小时候开始有比较明显的影响(会导致强度下降约0.5MPa),8小时候物料会逐渐变硬结块;因此半干法出转晶器的物料*好在4小时以内进入烘干设备进行烘干,生产工艺设置上转晶器与烘干设备的衔接时间以小于4小时为宜。
粉磨 转晶后的晶体,大小相对较为均匀,颗粒变粗,比表面积变小,活性降低。如果不经过粉磨,产品凝结时间很长,强度上升速度很慢,不利于应用,因此,粉磨是**产品应用性能指标重要环节之一。不同的粉磨设备,对粉磨过程调整物料颗粒级配,达到*佳产品性能很重要。一般,球磨机对转晶物料粉磨的效果要好于其它粉磨设备。
混合蒸压转晶工艺的特点:
⑴原料适应性强 该方法可适用于粒度小于5mm、附着水含量小于20%、二水硫酸钙含量大于85%、成分稳定的各类石膏原料;
⑵石膏原料以粉状直接与转晶剂溶液混合均匀即可,不需要配浆、不需要造粒;
⑶转晶设备容积率高,易于规模化生产 物料以湿粉状态装入转晶设备,装入量可达到设备容积的80%,单台设备产量大,利于规模化生产;
⑷转晶过程物料为半干状态,不需要搅拌,仅需要保持合适的饱和水蒸气压力、温度、时间即可,过程简单易控;
⑸能够形成以短柱状晶体为主体的具有一定晶型级配和晶体粒度级配的混合型晶体,有利于提高产品性能指标;
⑹转晶过程基本无废水排放,转晶完成后不需要进行洗涤处理等工序,不产生大量废水,不需要进行废水处理,主要排出为水蒸气冷凝水,可收集利用;
⑺生产成本低,利用提高产品竞争力。直接生产成本主要由原料成本、蒸汽成本、转晶剂成本、电成本构成;
⑻生产线投资低,混合蒸压转晶半干法工艺,生产线主体设备均采用常规建材类设备,仅蒸压转晶设备部分要求较高,因此,整体生产线投资相对水热法等工艺大幅度下降;
半干法(混合蒸压转晶)生产α石膏晶体图片:
2、水热法
水热法是采用由一定浓度的转晶剂配置的溶液作为介质,与石膏原料配置成一定浓度的料浆,通过给料浆一定的温度和压力,使石膏在转晶剂溶液、温度、压力的作用下完成晶体的转化,形成特定形状(短柱状)的晶体;水热法工艺一般都具有原料配浆、转晶、浆料分离、洗涤、烘干、粉磨等工序;水热法根据转晶压力要求又分为带压水热法和常压水热法二类。
1)带压水热法
带压水热法一般是将二水石膏与特定的转晶剂一期配置成一定浓度的料浆,料浆浓度一般在20-35%(料浆浓度越低,越有利于转晶效果,但产量越小,料浆浓度越高,越有利于产量提高及成本降低,但不利于转晶的均一性),将料浆送入转晶设备内,通过对转晶设备内料浆加热,使料浆保持一定的温度和压力(一般采用0.2-0.5MPa的压力和130-150度的温度),并对料浆进行搅拌,避免料浆沉淀 ,在一定温度和压力及转晶剂溶液的作用下,二水石膏进行溶解再结晶,因为转晶剂离子的作用,形成特定的短柱状晶体。转晶完成后,通过对料浆进行离心过滤等方式将浆料分离,为了避免残余转晶剂对产品的影响,可以对过滤后的物料进行洗涤过滤,然后将处理完成后的含有一定附着水的物料送入烘干设备进行烘干,烘干后的α型半水石膏熟料经粉磨后既为成品。为了避免水污染及节省成本,一般需要对分离出的溶液进行调整后再次配置料浆利用,但一般在副产石膏中,因石膏中的多种可溶性成分会不断溶入溶液中,不断积聚,导致溶液中的各类离子浓度及成分不断改变,多次应用后会对转晶逐渐产生影响,因此,必须针对不同的原料设置合理的循环利用及水处理措施,增加水处理措施会大幅度增加生产成本。
2)常压水热法
常压水热法的生产工序基本与带压水热法相同,不同之处主要是转晶采用的条件为常压状态,转晶温度一般为95-105度,转晶剂溶液一般采用盐溶液,溶液浓度也远比带压水热法的溶液浓度高,二水石膏在较高浓度的盐溶液中,通过一定的温度完成溶解再结晶过程。因为采用的盐溶液浓度较高,因此必须对分离后的物料进行洗涤,同时对洗涤及过滤后的溶液进行再利用,因过滤洗涤后的溶液的溢出现象,会大幅度增加废水处理量及成本。宁夏建材研究院在2007-2009与浙江大学等单位合作完成863项目中试中,利用该方法生产的脱硫石膏原料α高强石膏粉,基料性能指标可达到2小时抗折强度6-7MPa,改性后可达到10MPa以上,具有较高的性能指标;
水热法生产α石膏晶体图片:
三、几种α型高强石膏生产工艺的产品性能及成本对比分析
宁夏博得石膏研究院(原宁夏石膏设计研究院)在高强石膏技术、工艺及设备方面具有较长的研究历史和积累,以上各类α型高强石膏生产方法及工艺均有涉及(研究及推广),并且干法技术及设备、半干法(混合蒸压转晶技术)技术及设备形成了自己独特的专利技术和设备;带压水热法也进行了大量的研究实验及小规模的生产技术及设备转让。对于各工艺方法的优缺点及产品性能特点,进行了大量的试验对比,不同的技术方法对原料的适应性存在一定的差异,不同的技术方法生产的产品性能也存在一定的差异,同时,生产成本更是存在很大的不同。以下,仅从我院在同一种原料下,不同技术方法的产品性能及成本方面进行对比分析。
1、不同技术方法生产产品的主要性能差异
该差异主要体现在干法其它生产方法上,干法生产技术直接采用块状石膏蒸压生产α型高强石膏,生产过程中不采用转晶剂,没有对晶体形状进行干预,晶体多为针状或簇状纤维晶体,产品标准稠度与其它方法相比较高,抗折强度高,可与其它方法处于同一水平,但产品抗压强度低于其它方法;半干法(混合蒸压转晶)生产的高强石膏与水热法生产的高强石膏性能指标基本一致,指标主要取决于转晶技术水平和生产控制等工艺方面。我院采用的96%左右的天然石膏及96%左右的高纯度副产石膏采用不同的方法生产的α型高强石膏性能指标对比如下表:
2、生产成本对比分析
α型高强石膏的生产成本主要由原材料直接成本、人工成本、投资成本、管理经营成本等构成。其中人工成本、投资成本、管理经营成本受生产规模、原料特性、产品类别、市场销售、总体投资等影响较大,各生产线直接可比性不强;而生产中的原材料直接成本是各种生产方法对比较为直接的部分,各种α型高强石膏的原材料消耗及成本对比如下(仅供参考):
在规模化生产中,产品性能指标会受到原料、生产控制、技术、工艺等因素的影响,而生产成本也会受到生产方法、原材料价格、生产规模、投资、市场、经营等因素的影响。高强石膏产品因应用领域众多,性能要求不一。因此,在实际生产中,应该根据自身原料特性(纯度、杂质、颜色等)、产品市场定位、生产规模等,选择能够发挥原料*佳性能和*低生产成本的工艺方法,以适应产品档次梯级分布的市场需求模式。
联系电话:13709572223 1256441197@qq.com
地 址:宁夏银川市绿地企业公园D区32号楼